Progressive Stamping of an Aluminum Damper Cover for the Aviation Industry
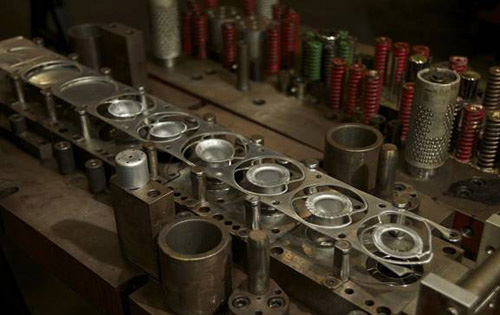
PROJECT DESCRIPTION
ART Metals Group was approached by a customer in the aviation industry that was looking for an alternative source for these aluminum damper covers. The material cost of having them CNC machined was very high, and they were interested in finding out if a part of equal quality could be produced using a less expensive stamping or coining process. We determined that making a slight change to the material specification would allow the use of progressive stamping.
We produced prototypes that were within the resonating frequency specified by the customer. This characteristic is critical to the functionality of these noise-reducing parts. Testing revealed that performance surpassed expectations, and we were able to supply a superior quality part at a huge cost savings to the customer.
Utilizing our 400 ton straight side press, we manufacture these 1.450″ high by 1.5″ diameter deep drawn stampings to within tolerances of ±0.005″. After deburring, parts are anodized for increased corrosion and wear resistance. Rigorous quality control ensures all specifications are met. We currently ship 50,000 of these units to the customer every year. For more information about this project, or how our progressive stamping services can economically supply you with precision aluminum parts, contact us today.
Highlights of this Progressive Draw Stamping Project
This part is used as a sound deadening device in airplanes.
Primary:
Progressive Draw Stamping
Progressive Stamping
Secondary:
De-Burring
Anodizing
400 Ton Minster Straight Side Press.
Height: 1.450
Diameter: Ø1.500
± 0.005
Aluminum
Control Plan, Dimensional Inspection
Aviation Industry
50,000 per Year
16 weeks
Customer Specifications, 2D CAD Drawing
Tuned Damper Cover
The amount of material required to CNC machine these Damper Covers, lead the customer to look for other options. They approached ART Metals, hoping that we could determine a way to make this a stamped or coined product. We quickly noted the material type needed to be changed to deep drawn quality aluminum. Once the customer agreed with the slight material change, ART produced prototypes for customer testing. The test was for resonating frequency, as the part function is to reduce noise. The customer’s tests were surpassed and we built a progressive deep draw die. The customer is ecstatic with quality of the part, and the huge cost savings in both material and machine time. This project was chosen, as an example of ART’s ability to reduce cost and improve process, which helps customers to hold or gain market share. Producing the same high quality part at reduced costs.